Featured NewsMiscellaneousTyto Robotics Pursues Bigger and Better Motor/Propeller Testing
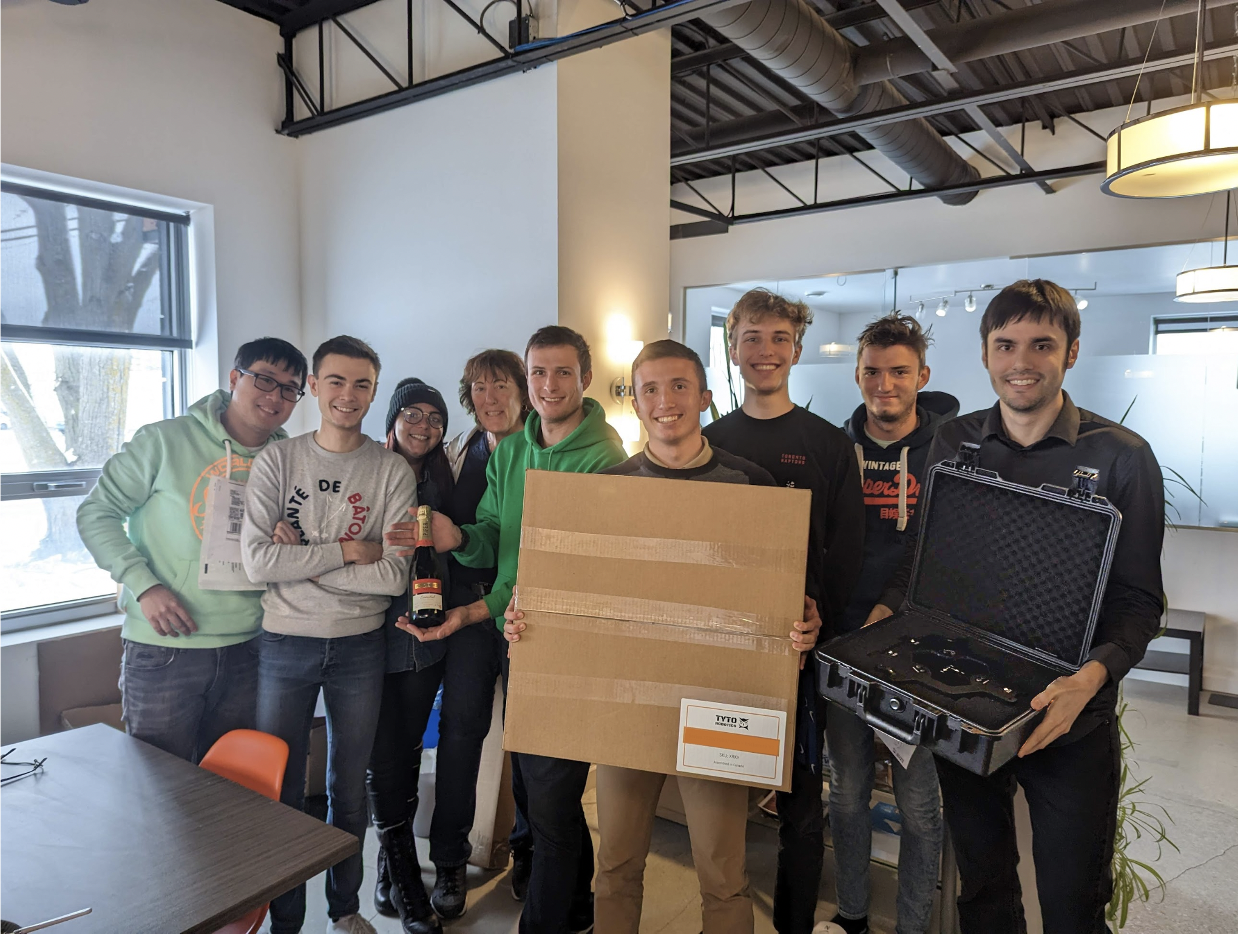
Above photo: The Tyto Robotics team displays components of the Flight Stand 150.
22 December 2022
Tyto Robotics recently shipped their first Flight Stand 150 test stand.
In 2014, the company—then called RCbenchmark—sold its first piece of equipment—a 5kgf thrust stand called the Series 1580. Fast forward to today, and they have just shipped the Flight Stand 150, which can measure a whopping 150kgf of thrust.
It is both the largest test stand Tyto has ever built and the world’s largest off-the-shelf thrust stand for motor and propeller testing.
Why Propulsion Testing
When Tyto co-founders Charles Blouin and Dominic Robillard were Masters students at the University of Ottawa, they wanted to design a miniature, hand-held helicopter. Their first iteration was manually controlled, and it used the airframe of a coaxial helicopter. It flew fairly well, but the coaxial design made it very unstable in windy conditions—plus it was noisy.
The biggest ongoing issue was that the electronics were too heavy, and the brushless motor was very inefficient. The result was a flight time of only three minutes.
They decided to build a DIY thrust stand/dynamometer to better understand what was going on with the motors. They ended up going down the rabbit hole with this side project, and built several versions of the test stand.
In the end, the DIY stand was able to help them find a more efficient motor/propeller combination, and they more than doubled the flight time of their helicopter.
While working on the DIY thrust stand, they started to see some interest from colleagues and researchers wanting a stand for their own research. This is when they realized that there was a real need for testing tools for UAV designers.
They named their first 5kgf thrust stand the Series 1580, then released the Series 1780 25kgf a few years later, then the 40kgf, and, finally, the 75kgf version in 2019.
In 2022, they shipped the first Flight Stand 150—a stand 30 times bigger than the original Series 1580.
Check Out the Flight Stand 150 User Video
What Motors and UAVs Can the Flight Stand 150 Test?
The measurement limits of the Flight Stand 150 were selected with two things in mind: the types of motors that clients needed to test and the size of UAVs and eVTOL the stand would serve.
By interviewing clients and performing independent research, Tyto’s team created a list of motors that clients would likely need to test. A few motors that made the list include MGM COMPRO’s REB 30, EMRAX’s 208, T Motor’s U15XXL, NeuMotors’ 12030, and MAD Components’ M50C35.
This short list of motors also allowed them to design a motor mounting plate that would fit most motors. The mounting plate is used to secure the motor to the test stand while aligning it with the necessary probes and ports.
The Flight Stand 150 mounted with Xoar TA180 motor.
The next step was to create a list of UAVs and eVTOL that generated thrust greater than 75kgf per propeller—thus requiring a larger test stand than the Series 1780. Aircraft that made the list included UAVs or eVTOL with a MTOW corresponding to ≤150kgf per propeller, so 600kg MTOW for a quadcopter or 1200 MTOW for an octocopter.
Dual Motor Testing
The Flight Stand 150 was also designed to permit testing of dual motor and coaxial rotor designs, since they are very common in UAVs and eVTOLs. Front-to-front, back-to-back, and offset rotor testing is possible. With two motors, the combined forces measured for the whole system can be up to 300kgf for thrust and 300Nm for torque.
A back-to-back dual motor testing set-up.
What Features Are New?
The Flight Stand line of test stands is designed to succeed Tyto’s Series 1780 test stand, which measures up to 75kgf of thrust and 48Nm of torque. The Flight Stand 150 was built in parallel with Tyto’s other Flight Stand test stands, which offer a 1,000Hz sampling rate, general analog inputs, monoblock load cell and ASTM calibration.
1,000Hz Sampling Rate
The 1,000Hz sampling rate means that users can obtain real-time dynamic data from their tests. More specifically, it means that the timestamps associated with the measured values exactly match the timestamp at which the analog measurement was taken on the circuit board.
This feature provides many opportunities:
- Precise current and voltage analysis (visualize sinusoidal patterns).
- Propeller vibration testing.
- Reaction time analysis.
- Accurate flight replay with controller data.
General Analog Inputs and Probes
The stand offers two general analog input ports, so users can connect whatever probes they need, such as pressure sensors, humidity sensors, vibration sensors, etc., up to 10V. The stand also comes with two PT100 temperature sensors that measure -30 °C to 100 °C, and one optical RPM probe for measuring motor speed.
Input ports on the Force Measurement Unit.
Custom Monoblock Load Cell
Using a monoblock load cell means that there are no moving parts in the force measurement unit—no bearings or hinges that introduce unwanted and random friction. The load cell is custom designed to provide the proper ratio of thrust/torque measurement so both forces are precisely measured within the desired range. The load cell casing is also designed to minimize airflow restrictions while maintaining a minimum thickness in order to test coaxial systems.
ASTM Calibration
The stand is calibrated using the ASTM E74 standard for thrust measurement (339 points) and an internal standard for torque calibration (204 points). This feature is a highlight for companies who seek certification of their aircraft and need referenceable data. Additionally, the stand undergoes a 1,044-point crosstalk calibration to ensure there is no interference between thrust and torque measurements.
What This Means for the UAV and eVTOL Markets
What makes the Flight Stand 150 unique is that it is an off-the-shelf product. Once an order is placed, it is shipped in just a few days.
While there are benefits to designing a custom test stand, the wait times often extend to weeks and months, meaning UAV designers have to wait a long time before getting the data they need.
Similarly, designing a test stand in-house can take up time and resources that would be better used elsewhere. Dominic Robillard, co-founder and CTO of Tyto Robotics, says that each year they have clients come to them after having attempted to build their own test stand. Some of these clients have some success, but many mention the resources invested were not worth it, as they lost focus on the main goals of their project.
With the Flight Stand 150, UAV and eVTOL builders can have the stand within days of realizing their need, causing minimal interruptions in the design process. In this highly competitive industry, time to market is crucial.
Where the Industry is Going in the Next Ten Years
Charles Blouin, President of Tyto Robotics, sees a bright future for electric aviation and UAVs. ‘’We see a clear trend in the industry: UAVs are getting better every year. They fly longer and with better software. The business case for many applications depends on flight time. UAV and eVTOL manufacturers need to put much more effort into optimizing their powertrains than in 2017. We are going to keep innovating to provide our customers with tools that help them fly longer and get their products to market faster.’’
Tyto Robotics president Charles Blouin standing next to the Flight Stand 150.
About Tyto Robotics
Tyto Robotics is a Canadian aerospace company specializing in the development of professional testing tools for drone characterization. Founded in 2014, the company manufactures several varieties of test stands that fully characterize brushless motors and propellers for drones and eVTOL aircraft. Thousands of companies across the globe have benefited from Tyto Robotics’ products, including NASA, Airbus, Volansi and numerous prestigious research institutions.